Expanding Wesgar’s sustainability program.
While we have implemented various initiatives over the years to minimize the environmental impact of our manufacturing processes, such as improving the energy efficiency of our manufacturing facilities to increasing our waste diversion rate, Wesgar, has now committed to further its sustainability goals by working towards decarbonizing its value chain. One significant step towards this endeavor has been the transition from traditional lighting systems to energy-efficient LED lights within Wesgar’s manufacturing facilities. This switch not only reduces energy consumption but also aligns with the company’s goal of minimizing its environmental impact. By embracing LED technology, Wesgar not only enhances its operational efficiency but also contributes to mitigating greenhouse gas emissions associated with energy usage. Moreover, Wesgar has integrated an in-house nitrogen gas generator into its manufacturing processes. This innovative technology allows the company to minimize its reliance on external sources for nitrogen supply, thereby reducing transportation-related emissions and promoting resource efficiency. By generating nitrogen on-site, Wesgar, as a sheet metal fabricator demonstrates its commitment to sustainability by minimizing the carbon footprint associated with nitrogen production and transportation. In 2023, Wesgar launched its carbon management program by measuring its greenhouse gases (GHGs) for Scope 1 and Scope 2 emissions. Now, we are well underway addressing our Scope 3 emissions as part of our second GHG inventory. By identifying Wesgar’s business activities that are contributing to climate change and measuring our carbon emissions, we are positioning ourselves to effectively optimize our processes to further reduce our environmental impact.
In recent years, there has been a significant global push towards greening industrial sectors, and we have seen an increasing demand for greenhouse gas data from our customer base. As a key supplier to large enterprises who are working on decarbonizing their supply chain, it was important for Wesgar, as a sheet metal fabrication manufacturer, to not only further develop its environmental sustainability program, but also support its customers with their sustainability goals along the way.
What is green manufacturing?
The manufacturing sector consumes large amounts of energy and resources in its processes, and consequently emits significant quantities of greenhouse gases. This increases environmental issues such as climate change and environmental degradation. Green manufacturing offers a pathway to reduce a manufacturer’s environmental impact by implementing various optimization processes to minimize waste and pollution.
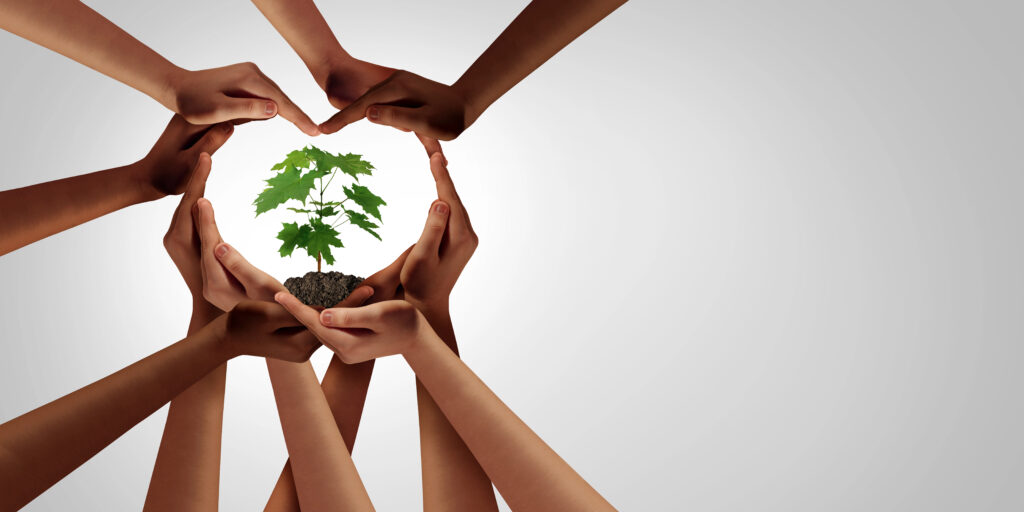
What is Scope 1, Scope 2, and Scope 3 greenhouse gas emissions?
Greenhouse gas (GHG) emissions are classified into three mutually exclusive emission source categories to avoid double-counting emissions across an organization’s value chain.
Scope 1 relates to emissions that are directly emitted in an organization’s owned or controlled sources, such as an HVAC system that burns natural gas as a source of heating for the company’s facilities.
Scope 2 emission are indirectly emitted by an organization consumption of purchased electricity, heat, or steam. Here, while the emissions are released at the electricity, heat or steam utility facility, these emissions are directly related to the organization’s consumption of energy.
Scope 3 relates to all other GHG sources occurring upstream and downstream of the organization’s supply chain. While only Scope 1 and Scope 2 emissions must be reported in a GHG inventory, it is best practice to include relevant Scope 3 emissions to fully capture a company’s carbon impact.
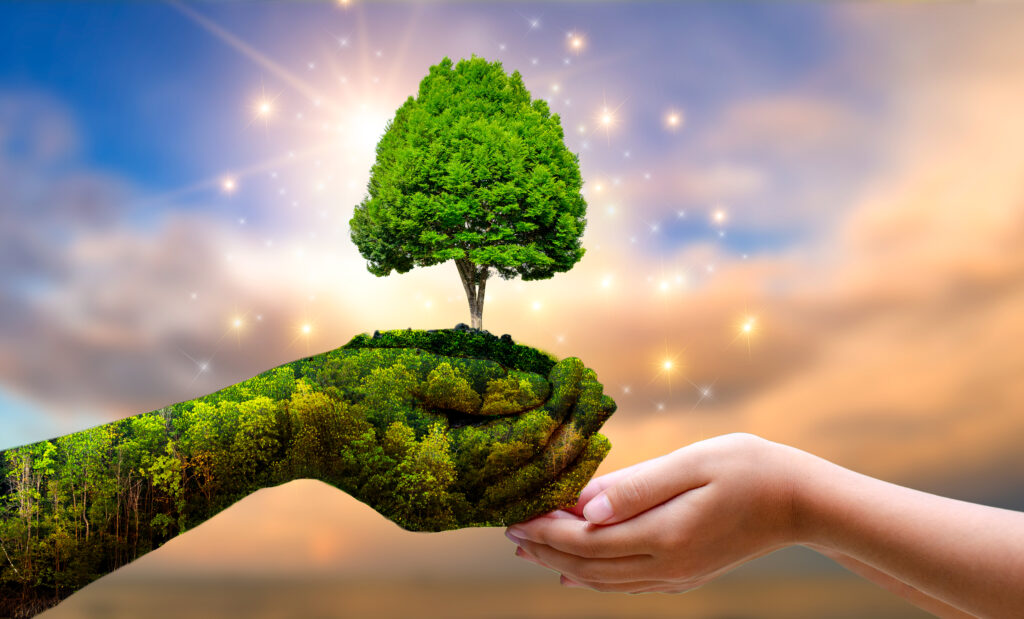
As we continue on our journey towards a cleaner, better planet for all, we invite like-minded companies to partner with us. Together, we can collaborate on innovative solutions and support each other’s sustainability efforts. Reach out to us today, to see how we can support your next project.