The constant evolution in manufacturing processes and the increasing demand for cost-effective methods have driven many companies to rethink traditional manufacturing methods. One way companies can save money while being more efficient, is the conversion of manufacturing parts to sheet metal. Sheet metal fabrication offers tangible cost-saving advantages, improved production timelines, and superior versatility compared to traditional manufacturing methods.
Reasons to consider sheet metal fabrication
Manufacturers that employ Supplier Kanban have one aim—to ensure a demand-driven supply of parts to their customers. It’s a highly effective method used to increase delivery reliability and reduce replenishment lead time.
Cost Efficiency
The primary reason to consider converting your manufactured parts to sheet metal is, of course, significant cost savings. Modifying existing parts to your needs is expensive and doesn’t usually give you the results you want. Sheet metal, on the other hand, can be customized as needed, allowing for greater flexibility. In addition, you don’t need to use molds, and, at Wesgar, we can usually use existing processes, tools, and machines that are already available to us, which results in even more cost efficiencies.
Versatility
Many customers are surprised at the versatility sheet metal offers. It can be cut, bent, and shaped into virtually any form, making it suitable for a wide range of applications across a number of fields. Additionally, if you are converting from fiberglass cabinetry, sheet metal will provide more internal room for the finished enclosure, due to the fiberglass casting process requiring a tapered mold.
Generally, the more we know how the part will be used, the easier it is for us to customize it. For example, we can thicken a part to make it more durable, we can make it airtight, lighter if weight is a factor, or more refined if it’s customer-facing. For those designers or engineers who don’t work with sheet metal on a daily basis, you will likely be surprised to learn how many different applications there are.
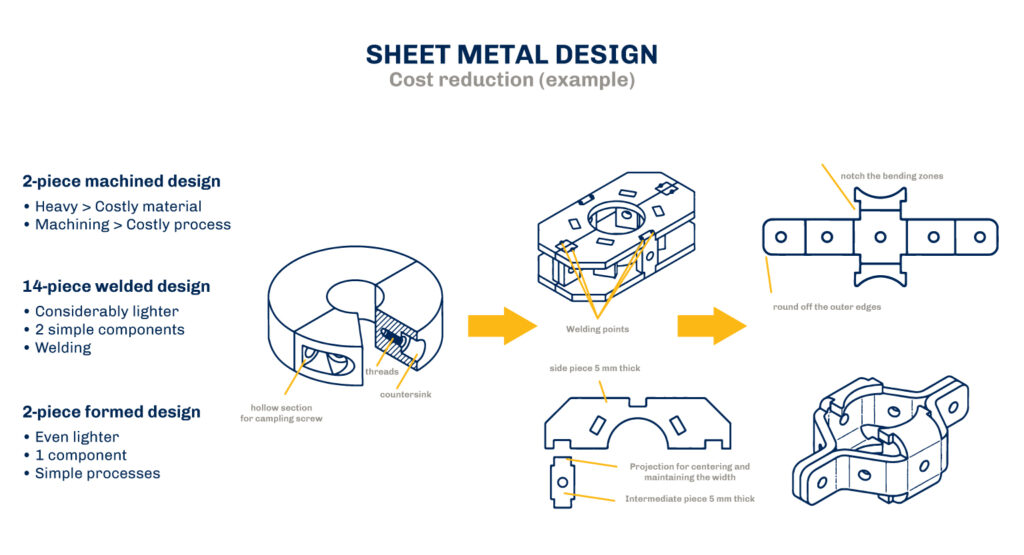
Speed and ease of production
The sheet metal fabrication process is extremely time efficient—especially for a company like Wesgar that has everything on hand to convert manufactured parts into sheet metal parts. Another process that might be considered is 3D printing, which is becoming increasingly popular, but sheet metal is generally faster, cheaper, and more reliable. In addition, 3D printing is limited by the size of the actual printer you have, whereas sheet metal manufacturing allows for much larger components, often up to 5 feet x 10 feet raw sheet size.. We can create hinge features, punch holes, create dimples, threaded holes, and other critical features as necessary without adding labor-intensive steps.
Durability
Durability may not be the first thing that comes to mind when you think about sheet metal. However, sheet metal, despite being lightweight, is incredibly durable and can withstand harsh environments. Additionally, sheet metal parts can be manufactured to be resistant to high temperatures, pressure, and corrosion, making them ideal for long-term applications. If necessary, we can also thicken the sheet metal or reinforce it to make it even more durable.
How to convert your manufactured parts to sheet metal
The first step is to figure out what parts can be replaced by sheet metal manufacturing. Some common parts are brackets and machine enclosures. If you are unsure whether sheet metal can be an appropriate replacement, talk to us. Generally, the earlier you include us in the process, the more we are able to guide you, offering suggestions, and supporting your design and engineering team. We offer this as a complimentary service to help increase the speed of your process, which can save you money and produce your part quicker.
Next, review your existing part’s design. Identify the function of the part and how its form can be adapted to a sheet metal design. Working with us in the design phase is incredibly important to help streamline the process and ensure the part is built exactly to the needed specifications.
The last step is the fabrication process. At Wesgar, once we know what we are building, we have the tools, the machines, and the knowledge in order to build a part that meets all the required functionality.
Free workshops on converting your manufactured parts to sheet metal
Wesgar offers free half-day workshops to guide you and your team through a step-by-step process on how to get started. Our workshop includes a tour of our facility, and you’ll see real-life examples of how sheet metal can be used, see what is possible, and give you new ideas. We are certain creative solutions will emerge. If you’d like to schedule a seminar, please don’t hesitate to contact us.
Wesgar is experienced in converting manufactured parts to sheet metal
Efficiency, cost-effectiveness, and flexibility are paramount to successful manufacturing, and converting your manufactured parts to sheet metal can be a game-changer. It provides a host of benefits, from cost savings to improved production times, increased durability, and enhanced versatility. With careful planning and partnering with knowledgeable fabricators, the process can be smooth and rewarding. Wesgar’s team of engineers is experienced at helping customers convert manufactured parts to sheet metal and cutting costs. So contact us today and let us know how we can help.