At Wesgar, we aim to deliver first-class quality products to our customers consistently, and to achieve this, we deploy a combination of tools and processes such as quality plans, failure mode effects, analysis, and in-process inspection, to name a few.
High-quality products at a competitive price
Quality is a top priority for everyone at Wesgar. Our quality management system is ISO 9001:2015 certified (updated May 2021).
Continuous improvement
Our quality system heavily emphasizes input from plant personnel. We encourage all staff members to identify issues and or opportunities for improvement in our production processes and make improvement suggestions. Change requests submitted by team members often result in improved part quality or an efficiency gain in a process. We’ve built an infrastructure that facilitates and rewards continuous improvement and problem-solving. Our fabrication experts thrive on these challenges.
Integrated waste reduction and cost reduction
Our manufacturing processes are designed to reduce waste and total part cost. Our product support team continuously identifies where focused resources will provide the maximum payback. We examine details such as material specifications, product design, ordering methods, level of inspection, stocking programs, and packaging requirements. We pass reduced costs as a result of these measures to our customers.
Controlled inspections
Stringently controlled inspections are carried out by our fabrication specialists and our quality inspectors.
- First-off checks
- First Article Inspection (FAI)
- Production Part Approval Process (PPAP)
- Quality Plans
- Failure Mode and Effects Analysis (FMEA)
- Statistical Process Control (SPC)
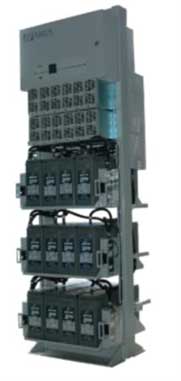
“Quality is free. It’s not a gift, but it is free. What costs money are the unquality things—all the actions that involve not doing jobs right the first time.”
—Philip B. Crosby, Businessman, Author, and Initiator of the Zero Defects Program