Powder coatings have become the preferred finish for many industries, used in heavy equipment, marine transportation, electronics, outdoor recreational products, appliances, and more. Compared to liquid coatings, the key benefits of powder coatings are a solvent-free work environment, lower production costs, and simple cleanup.
What is powder coating?
As a dry finishing process, powder coating uses electrostatically charged ground particles of pigment and resin sprayed onto metal products. The charged powder particles adhere to the surfaces until heated and fused into a smooth coating with the help of a curing oven.
Is powder coating right for your sheet metal component?
Now, if you’re tasked to purchase powder coating for your company, you’ll want to promote efficiency to avoid powder coating waste and, ultimately, increase your organization’s profitability. So here is some helpful information and guidelines to follow before deciding.
Why invest in the powder coating process?
Powder coating is a superior finish option for various applications due to its durability, resistance to corrosion and abrasion, and ease of application. The versatility of powder coating also allows for a wide range of color and texture options, making it a suitable choice for many sheet metal components.
How to choose either a powder coating or a wet painting finish
The choice between powder coating and paint finish depends on the specific requirements and intended use of the coated component. For high wear and tear applications, powder coating is often the preferred option due to its superior hardness and resistance to chipping, fading, and weathering. This makes powder coating popular for industrial components exposed to harsh environments.
On the other hand, paint finishes are often preferred for aesthetic reasons, as they offer a wider range of colors and textures and can be applied to achieve a smooth, glossy finish. In addition, paint finishes can be used in applications where the durability of the coating is not a primary concern, such as for indoor rooms or structures protected by the elements.
Is the powder coating process compatible with all manufacturing processes?
The powder coating process can be incorporated into the fabrication of a wide range of sheet metal components. However, certain factors, such as the size and shape of the component being coated, the type of substrate, and the desired finish, can affect the compatibility of the powder coating process with a specific manufacturing process.
For example, components with intricate shapes or tight tolerance requirements may not be suitable for powder coating, while others may require specialized equipment or techniques to achieve a high-quality finish. It is important to work closely with your powder coating supplier to determine if the powder coating process is compatible with the manufacturing process and what modifications, if any, may be required to ensure a successful outcome.
What is the cost per unit of powder coating compared to alternatives?
This can depend on several factors, including the size and complexity of the component, the type of substrate, and the desired finish. In general, powder coating is a cost-effective finishing option compared to traditional liquid coatings, particularly for high-volume production runs. This is due to the high transfer efficiency and low material waste associated with the powder coating process, as well as the ability to automate many aspects of the coating process, which reduces labor costs.
What is the environmental impact of the powder coating process, and are there any regulations to consider?
Powder coating is generally considered to be a more environmentally friendly option compared to traditional liquid coating processes, as it produces less hazardous waste. However, it is important to consider the environmental impact of the powder coating process and comply with any relevant regulations. The production of powder coating materials and the operation of powder coating facilities can have impacts on air and water quality, as well as the generation of solid waste.
The release of volatile organic compounds (VOCs) from the curing process can also contribute to air pollution. To minimize these impacts, powder coating facilities should implement best practices such as using low-VOC powders, implementing efficient waste management systems, and regularly monitoring emissions. Additionally, regulatory compliance must be considered, including civic, provincial, and federal regulations related to air and water quality, as well as the handling and disposal of hazardous waste. To ensure that these requirements are met, it is important to choose a powder coating supplier that takes environmental concerns seriously and operates in accordance with the most updated environmental practices.
A few best practices to check before selecting your powder coating provider
Powder coating durability
Improper curing of powder coating can result in poor adhesion, chipping, and decreased durability. The bake schedule is set by the manufacturer and should be followed to produce the most durable and longest-lasting finish.
You can determine if a part has been cured properly by doing the “scratch test.” To do this, use your fingernail to scratch the surface of the coating. If the coating comes off easily, it has not been cured properly.
The importance of storing powder coating materials correctly
Poor storage of powder coating materials can lead to clumping, caking, and moisture contamination if not done properly. Powder coatings must be stored in a dry area with ample ventilation. It must be away from any sources of heat or ignition. The ideal storage temperature must be below 80 degrees, while humidity is preferably at less than 50%.
Powder coating success depends largely on the maintenance of powder coating equipment
Preventive maintenance practices play a vital role. To ensure the longevity of powder coating finishes, equipment should be cleaned and inspected regularly. If the factory floor is unclean, or the equipment is ill-maintained, the powder coating quality will likely be sub-standard.
How to maintain powder-coated components
After applying powder coating, proper maintenance is essential to ensure the longevity and appearance of the surface. To maintain the integrity of the coating, surfaces should be cleaned regularly using a soft cloth or sponge and mild detergent. Abrasive materials or harsh chemicals should be avoided as they can damage the surface of the coating.
In case of scratches or chips, it is advisable to touch up the affected area promptly to prevent corrosion or rusting. Regular washing and wiping down surfaces of outdoor applications can help to prevent the buildup of dirt, grime, and other environmental pollutants that can deteriorate the coating over time.
Wesgar is an experienced high-quality powder coater
There are many factors to consider when selecting a powder coating provider, including the provider’s experience, expertise, and capabilities. It is essential to look for a provider with a proven track record of delivering high-quality powder coating services with a focus on customer satisfaction and meeting specific requirements.
The Wesgar team has a reputation for craftsmanship, precision, and innovation. We utilize these principles alongside our cutting-edge powder coating technologies to ensure you get the best powder coating results. So contact us today and let us know how we can help.
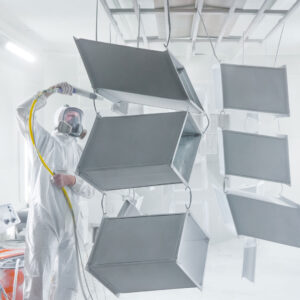